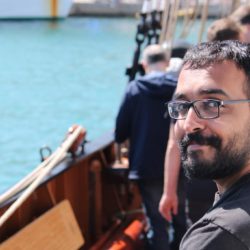
There are so many new technologies changing the current business landscape that at times it may be hard to keep up. While many people are familiar with Industry 4.0 and the Internet of Things (IoT) – both terms which refer to large collections of technology and their business applications – the Digital Twin is another approach that is steadily picking up traction.
In fact, many people see the Digital Twin as a natural successor to IoT. After all, if everything is already connected in some digital form or another, why not take it to its logical progression?
This, in essence, is the main drive behind Digital Twin architecture and technology – to entirely replicate the physical world in a digital landscape, giving companies new freedoms, opportunities, and advantages.
What Is A Digital Twin?
The Digital Twin concept, first proposed by Michael Grieves at the University of Michigan, has been around since 2001, but it is only in recent years that modern technology has made it a realistic opportunity.
Put simply, a Digital Twin refers to the virtual replication of a physical product or asset. This replication is updated in real-time (or as regularly as possible) to match its real-world counterpart as closely as possible.
This model can then be used for a variety of purposes, from testing new strategies to analysing previous results, which we’ll explore shortly.
So, how does this actually work? Generally, sensors and other components are used to gather accurate data about the asset in question. This data is then processed and used to create the replica. Needless to say, more advanced sensors, whether in the form of more accurate equipment or a denser, more compact array, will help towards creating a more detailed digital model.
What Are The Benefits Of Digital Twin Modeling?
Experimenting on physical products and assets can be a timely and costly process. A digital replica, however, can be quickly edited to test new solutions and to run simulations. If the experiment doesn’t meet the desired requirements, no physical resources have been wasted.
Another benefit to Digital Twins is that they allow experts to work on projects even when they are not in direct contact with the physical twin.
A great example of this can be seen at NASA, which has long been a pioneer of this technology – even before virtual simulations, engineers created 1:1 scale replicas of equipment sent skywards. Digital Twins allow engineers to work on equipment that’s already in space, and completely inaccessible to them, without the hassle and difficulties that come with physical duplications. Updates and alterations can be planned in exact detail and tested offsite, before instructing those with access to make the physical changes.
According to John Vickers, a manufacturing expert & manager for NASA’s National Center for Advanced Manufacturing: “The ultimate vision for the Digital Twin is to create, test, and build our equipment in a virtual environment. Only when we get it to where it performs to our requirements do we physically manufacture it. We then want that physical build to tie back to its Digital Twin through sensors so that the Digital Twin contains all the information that we could have by inspecting the physical build.”
Similarly, for companies that want – or need – to make changes to existing products or equipment, Digital Twins help keep downtime to an absolute minimum. Consider a production line, for example. An ineffective link can limit the optimal efficiency of the entire chain, yet it’s simply not possible to remove it entirely for review/assessment, as this would shut down the entire process that it is a part of. A virtual replica, however, can be tested and refined without incurring these costs.
Digital Twin & IoT
So why do we think the Digital Twin is the “next thing after the IoT”? Well, this is because the former flourishes on sensors and input data, which is something the latter is spreading more and more into our world.
With more interconnected devices and applications, it’s easier for organisations to interlink data and get a better view of the wider picture. A Digital Twin, then, is simply an advanced way of collecting and combining this data for specific purposes.
In fact, this is a revolution that’s already well underway. According to Gartner, 75% of businesses integrating with the IoT are expected to be using – or making plans to start using – some form of Digital Twin technology by next year (2020). It’s also estimated that 13% of companies are already using such solutions, with another 62% already in the process of adopting some form of Digital Twin.
Digital Twin Use Cases & Industries
One thing you will notice with many of these Digital Twin applications is that the best results work alongside other technologies, such as Artificial Intelligence or Machine Learning. Others, likewise, may use Digital Twin solutions as part of Industry 4.0 or the Internet of Things, building on previous innovations.
This is worth noting, as it isn’t a brand new, alternative solution. Digital Twin is used for improving existing processes, giving people a virtual playground of sorts to experiment and try various approaches in a simulated environment that won’t impact the real product until direct action is taken.
Digital Twin technology is used for a wide variety of purposes and most businesses have something to gain. However, there have been some strong Digital Twin use cases in certain major industries, which are worth exploring here.
Manufacturing & Engineering
Creating virtual replicas undoubtedly has clear benefits for the manufacturing and engineering industries. The role of Digital Twin in manufacturing requires little introduction. It enables firms to test new designs quickly and efficiently, whether it’s small products or large, complex equipment. Testing a new supply chain in a virtual setting is easy, whereas testing the physical equivalent involves shutting down production, losing profits as a result – something that should only be done when necessary and when the most optimal strategy has been determined.
Of course, such technology can do so much more than this. One interesting example of this is GE’s Digital Wind Farm. By using digital recreations of their wind farms, operators can produce optimised maintenance strategies, taking weather and other factors into consideration. All of this leads to improved reliability and an increase in the energy output produced, due to both improved maintenance and a better assessment of various conditions.
Because this is all done digitally, engineers are free to experiment and research, whereas making physical changes on actual turbines can be a costly expense. The former ensures that the latter is only done when the solution has been fully tested and assessed.
Of course, these benefits also apply to the production process. Factories and plants can use virtual replicas to test more streamlined solutions and discover the limits of their current production capabilities, as well as test the strain of new IT solutions for the manufacturing industry.
Automotive
We mentioned earlier that Digital Twin can use sensors to record the ongoing state of any project. Such Digital Twin analytics has plenty of potentials – not least of all in the automotive sector. As cars become more and more integrated with IoT and digital technology, the ability to replicate every detail becomes more and more accessible.
After any incident, for example, the Digital Twin can use sensor recordings to create a realtime replication of what happened. This way, engineers can directly analyse the effects on the vehicle at each exact moment, rather than just analysing post-recorded data.
Yet, the implications of Digital Twin’s automotive benefits go much further than this. Engineers can test new safety features in the digital world, reducing the risk that new vehicles don’t need to be recalled – a financially dangerous prospect for industries where individual units have high production values and costs.
This is also important in an industry such as the automotive sector, where parts and components are sourced from a multitude of different companies. The Digital Twin allows both suppliers and producers to gain more data, test new solutions and refine their products before they become part of the greater product.
Similarly, many smart car producers are testing self-driving AI in digital environments. Because this technology is still being developed, manufacturers can gain data through real-world tests, but refine and improve their solutions in the digital landscape as much as possible.
Even after the design stage, modern technology can be used to streamline the supply chain and manufacturing processes, greatly reducing the time and cost of production.
Healthcare
Furthermore, Digital Twins in the healthcare sector can identify faults or problems with the various equipment (which is often very expensive and needs to operate at optimum levels) involved in various medical fields. The likes of MRI scanners, for example, generate vast amounts of daily logs and messages, which can be fed into the Digital Twin to review its current status, as well as project emerging issues. With this, engineers can work on solutions for predicted problems ahead of time, avoiding critical issues and keeping such equipment well maintained.
On a more personal level, medical devices can also extend to the Cloud, where data from their sensors can be immediately correlated with a patient’s medical history, as well as external data – such as demographical figures. From this, it’s also possible to run Machine Learning analysis – something that wouldn’t be possible on the initial medical device – opening up greater insights that take in as much information as possible to provide additional insight, all powered by a virtual copy of each patient (at least from a medical data perspective).
For hospitals and medical facilities, Digital Twins can be used to stress test operations, simulating how best to operate during mass emergencies. Such organisations often have various components, from available staff, patient beds and access to various testing rooms, that can be refined to better handle more difficult situations.
Likewise, in terms of applying Digital Twin in direct healthcare products, such technology could also be used to assist doctors in providing unique, tailored care for individual patients. With enough information, Digital Twins can propose solutions more likely to work for each individual, taking their unique medical history and data into account.
In fact, due to all of this, many are betting on the healthcare sector to make the biggest gains from this technology, even if not right now. As the medical field becomes advanced and more accurate sensors, (such as genome reading), become more commonplace, the ability to combine all of this virtually will open up new possibilities for the industry as a whole.
Retail
The retail landscape is one that thrives on data, from the very start of a product’s manufacturing cycle to how it’s strategically displayed in store. It stands to reason, then, that employing a Digital Twin in retail businesses offers plenty of strong benefits.
At a product level, companies can use Digital Twin models to follow a product from its very inception through to in-store placement. Here, companies can analyse manufacturing processes, supply chains and logistics, testing new, streamlined solutions to cut costs (and consequently improve profit margins) behind the scenes. Want to test if a new packaging or design can reduce expenses? Digital Twin lets you test this without having to make large scale physical changes to your entire product range.
At a wider business level, retail stores can use Digital Twin technology to replicate their store and, using sensors, track customer behaviour. This information can then be stored on the Digital Twin to research the best placements for key products. Changes and layout alterations can then be suggested and tested digitally.
Amazon is already doing something similar to this, using analytical data to determine the best layout for its warehouses, with the most in-demand items stored in the most accessible locations. Digital Twins offer a great way to test such automation, ensuring proposed solutions don’t have unforeseen consequences, such as direct access channels or routes intercrossing and causing delays.
The Digital Twin City
So far, we’ve looked at various examples of machinery and equipment that can be replicated, assessed, and prototyped with a Digital Twin. Yet, when you think about it, it’s not a large stretch to also apply this concept to cities.
After all, cities have numerous moving, interconnected components. With a suitably advanced model, civil engineers, governments and other related companies, such as utilities, can better test new solutions. The likes of Paris, Cambridge and Toronto, for example, are actively developing Digital Twin city models for such purposes.
In fact, smart cities are already a growing concept around the world. Sensors are being installed to monitor as much data as possible, including traffic, environmental pollution levels, power demands and more. Singapore already has such a working solution, dubbed Virtual Singapore, which can be used to predict and calculate flood levels, wireless coverage, noise pollution, and even mosquito breeding conditions.
On a much larger scale, Digital Twin technology can replicate entire cities down to individually simulated components and use this to enable real-time two-way communication. For example, by analysing traffic as it develops – with each car, junction and traffic light simulated independently, this can be simulated ahead of time to predict where traffic will build up. The model, when paired with Machine Learning, can quickly test possible solutions and, once it has a working solution to an upcoming issue, it can send these control signals back into physical counterparts.
This way, you can establish a smart-AI traffic system that uses data to optimize traffic ahead of time – it can act predictively, not reactively. Because Machine Learning can learn from its own data, adding to the information, this entire system will continue to improve over time.
Best of all, such a solution – as well as the others mentioned here – can all be run on the Cloud, keeping the costs low, as the need for expensive hardware is no longer a factor that needs to be considered.
All of this serves to ensure new solutions are beneficial to the city and don’t come with unexpected consequences. Any new proposals can be simulated and, potentially, other companies can use this same simulation to develop products.
For example, we already mentioned how the Digital Twin benefits the automotive sector, earlier. With the rise of automated vehicles, it’s entirely possible for manufacturers to use simulated city environments to test their self-driving software in a risk-free space. This essentially gives them access to the entire city – a vast testing environment that isn’t possible in the real world.
How To Implement A Digital Twin
From a technological point of view, Digital Twin technology is becoming more and more accessible. Cloud technology offers a means to process and run simulations without expensive on-site servers, and Microsoft already offers a growing range of Azure Digital Twin products to help organisations in this objective, while Amazon Web Services (AWS) similarly offer a “Device Shadow” service as part of their AWS IoT lineup.
If your company has been embracing Big Data, IoT integration, or Industry 4.0 solutions, you’re likely already on the way to Digital Twin architecture. These technological trends all involve using sensors and other data gathering means to analyse and assess. In some cases, you may already have enough to create a prototype or working model.
Digital Twin Business Culture
That being said, implementing a Digital Twin does also require a strong digital culture as well. These models work best when businesses are already using sensors and other data gathering techniques to learn as much as possible – the Digital Twin thrives on updated and accurate information.
However, such changes can be implemented gradually. Introducing this technology in smaller steps, as an introduction or as an experiment, can help introduce staff at all levels, from engineers to business analysts, to this new approach.
A vital factor for any company, however, is identifying the areas you want to improve. Just like Big Data, it’s very easy to capture everything but there is no guarantee that it’s entirely useful. Such solutions should be refined and focused on their most applicable areas. This is one of the reasons why it’s best to start small, applying Digital Twin technology where it can be most beneficial. Diving into the deep end has its own risks, as it can overwhelm teams with an entirely new approach.
What is a Digital Twin – Summary
For many, the Digital Twin is already here – for others, it’s coming in the very near future. If you’re not part of the majority, it’s worth assessing your business and identifying areas where virtual simulations can provide a direct improvement. The IoT has already ensured the world – and companies in it – have access to a wide and varied source of sensors and input sources. Now it’s time to capitalise on that.
The Digital Twin enables companies to test new solutions, assess previous events, and predict future behaviour. It enables different companies to cooperate together on shared interests, as well as provide a low-cost, risk-free way to test new designs, solutions, and services.
Already used in a variety of industries, from the automotive sector to entire city planning, a Digital Twin, even at a very small scale of implementation, can bring many benefits and possibilities into your business.
Business Perspective
As the world becomes increasingly immersed with the Internet of Things, Digital Twin solutions are becoming more and more feasible. Such technology enables companies to assess, test, and improve freely, without having to worry about the risk factor. Furthermore, any real-world decisions will be reinforced by significant simulation results, helping organisations to make the best choices moving forward.
Sources
- What Is Digital Twin Technology – And Why Is It So Important?
- What Is A Digital Twin? [And How It’s Changing IoT, AI And More]
- Digital Twins
- How Do You Build A Digital Twin?
- Gartner: Digital Twins Beggining To Enter The Mainstream
- What’s A Digital Twin?
- IoT Digital Twins In The Consumer Retail Industry
- What Is The Potential Of Digital Twin Technology In Retail
- Why Will Smart Cities Need Digital Twins?
- Meet Virtual Singapore, The City’s 3D Digital Twin
- Cambridge Digital Twin To Tackle Congestion And Air Quality